Orchard Fencing Ltd Upgrades Precast Production with Bespoke Rapid International Concrete Batching Plant.
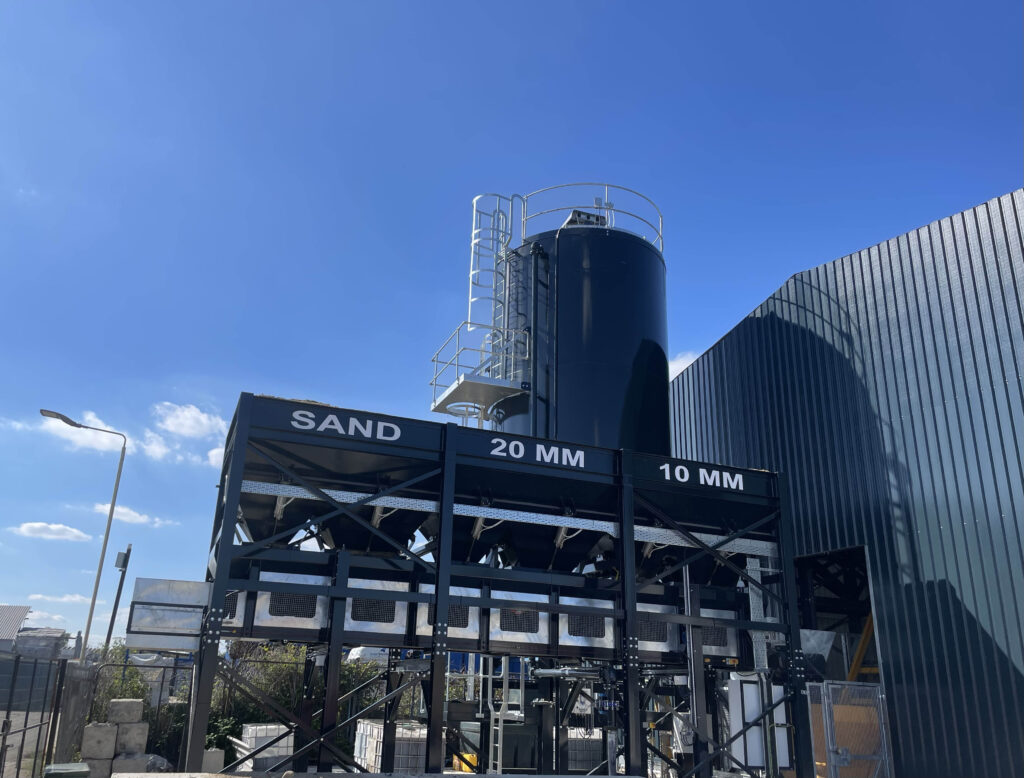
Rapid International Ltd (County Armagh, Northern Ireland) has recently supplied Orchard Fencing Ltd with a new bespoke static concrete batching plant, located in Erith, South-East London. The plant is capable of production of up to 22m3 per hour of concrete. Orchard Fencing aims to produce 1500 precast fencing products per day, in addition to interlocking blocks.
The upgrade project, at a cost of £2 million, also involved concreting the entire facility, new warehousing, reconditioning of the existing precast machines, two new forklifts and new Coote Engineering machines and moulds.
About Orchard Fencing
Established in Welling, UK, in 1989 by Neil Hubble, Orchard Fencing Ltd, under his leadership expanded its operations with depots in Catford, Welling, and Erith. Serving London, Kent, and the wider south- east area, the company specialises in retailing and wholesaling fencing products and aggregates. Notably, in 2012, Orchard Fencing supplied security perimeter fencing for the London Olympics.
Outdated plant required upgrade
Motivated to focus more on precast fencing products and confronted with an outdated plant over 30 years old, the company recognised the necessity to invest in new production facilities. Reflecting on this, George Hubble – Managing Director, remarked, “My grandfather Terry invested in a plant and a precast machine many years ago which served him well. However, as Orchard Fencing expanded, the old machinery simply could not keep up with demand. We knew that if we wanted to expand and improve our in-house precast production, that a major upgrade would be required.”
Concrete Technology
It was after a conversation with Coote Engineering, during the purchase of a Coote dry cast machine, that the company learned of Rapid International and their extensive experience in the design and manufacture of custom batching plants.
The company subsequently contacted Victor Pickering of Concrete Technology Ltd, Rapid’s GB mainland sales partner. Hubble added, “Victor was very helpful and knowledgeable. He conducted a thorough site visit, enquired about our requirements, and advised us on what specification of plant would best meet these. He then passed this information to Rapid’s in-house design team, who produced initial layouts, followed by 3D renders.”
He continued, “Victor also arranged a site visit to a previous customer of Rapid, Brett Landscaping, whose plant was installed 30 years ago and is still fully operational. Brett spoke highly of the plant. He also gave us a further 5 customer references, who we contacted, and who all spoke highly of Rapid.”
“Victor really put us at ease and together with Brett Landscaping, Coote Engineering and the five other customer recommendations, I felt confident that we were making the right decision and the plant was going to be good.”
The Rapid solution
Orchard Fencing’s new bespoke Rapid concrete batching plant offers outputs of up to 22m3 per hour. The new plant has three 12.5 tonne aggregate hoppers, with integral 600mm weighed belt conveyor, which discharges into a mixer loading skip. This skip subsequently feeds a 0.75m3 output Rapid RP750 planetary mixer, which is housed on a mixer platform with the production facility. The platform allows for maximum access for maintenance and cleaning at mixer level. On mixer maintenance, Hubble commented, “I find the Rapid mixer much easier to clean and maintain, with the fewer blades and no centre, compared to our previous German Pan Mixer.”
Two discharge chutes are located under the mixer doors to direct the material into the receiving hoppers on the Coote Engineering dry cast machines.
Cement is stored in an 80 tonne storage silo, with screw conveyor, which conveys material from the silo to the weigh hopper. A 500kg cement/powder weigh hopper is included, which is mounted on loadcells with aeration pads and a vibrator to aid in discharging. The plant also features a single compartment additive weigh system, which offers flexibility in additive batching.
To streamline mixer cleanout, the plant includes a Rapid Jetwash mixer washout system, fitted with 3 spray heads. The system operates at 2000 psi, offering high-pressure cleaning and maintenance of the mixer.
Enhanced control and productivity
The plant is fitted with a Pneutrol Dynamix batching control system, which enables the operator to oversee the entire batching process and offers unlimited recipe storage, manual control via the PC and remote operation. The plant controls are housed in an anti-vandalism control cabin, ensuring security.
Plant automation – user friendly
On the installation process, Hubble remarked, “We had a few minor issues at the start, but everything was taken care of by Keith (head of Rapid installation) and the installation team. Keith was brilliant and guided us through the whole process with organisation, attention to detail and precision. Everything has been no hassle and any minor issues we’ve encountered have been sorted via a quick phone call. Installation was very professional and streets ahead of anything we’ve encountered.”
On the plant, “We’re really pleased with it! We can now be totally self-reliant and have improved quality and service for our current customers and stockists. The new semi-dry machine requires a very accurate mix which would be very difficult to achieve without the Rapid static batching plant, the moisture probe inside the mixer calculates exactly how much water to add which gives us a fast, consistent and accurate batch every time.” “The steel work is heavy duty, unlike some of the alternatives in the market which can be really lightweight. It’s nice to see it’s been built properly and it’s clearly going to last. The automation is very clever and user friendly – PIL were excellent. Aftercare has been very good.”
Learn more about Rapid static plant here.
Read more static plant case studies here.
Contact us here.